CNC Turning Parts Manufacturer: Elevating Precision in Metal Fabrication
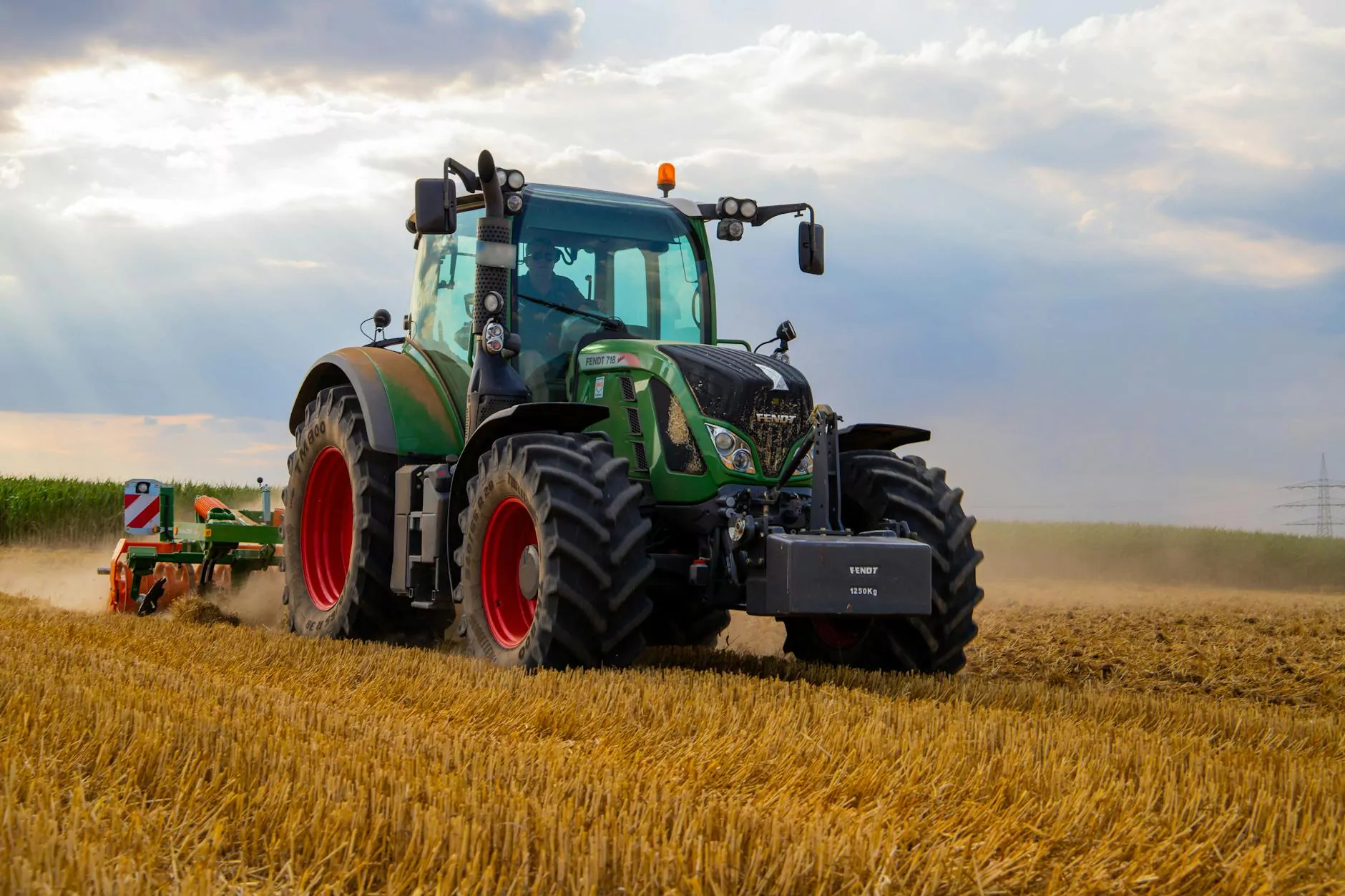
The modern manufacturing landscape is characterized by innovation and efficiency, and CNC turning parts manufacturers play a pivotal role in this evolution. By leveraging cutting-edge technology, companies such as DeepMould.net are setting new standards in precision engineering, enabling businesses across various industries to achieve their production goals with incredible accuracy. In this extensive article, we will delve into the intricacies of CNC turning, its advantages, the process itself, and the transformative impact it has on metal fabrication.
Understanding CNC Turning: A Technological Marvel
CNC turning involves a meticulous process aimed at producing precision components with intricate designs through a computer numerical control (CNC) lathe. This sophisticated machinery rotates the workpiece against a cutting tool that removes material, resulting in highly accurate parts. Here are some pivotal aspects of CNC turning:
- Precision: CNC machines can manufacture parts with tolerances as tight as ±0.001 inches, ensuring every component meets the highest standards.
- Efficiency: The automation of the CNC process allows for rapid production, significantly reducing lead times compared to traditional methods.
- Versatility: CNC lathes can handle a plethora of materials, including metals, plastics, and composites, making them suitable for diverse applications.
The Benefits of Choosing a CNC Turning Parts Manufacturer
Opting for a reputable CNC turning parts manufacturer comes with numerous benefits that contribute to the long-term success of your manufacturing operations.
1. Enhanced Quality Control
With state-of-the-art machinery and techniques, manufacturers maintain strict quality control protocols. Advanced equipment, such as coordinate measuring machines (CMM), ensures that every product is inspected for precision and consistency, preventing defects that could arise later in the production line.
2. Custom Solutions Tailored to Your Needs
Every industry has unique demands. A skilled CNC turning parts manufacturer can provide custom solutions that match your specific requirements. Whether you need a specialized component or unique geometric specifications, these manufacturers can adapt their processes accordingly.
3. Cost-Effectiveness
Although the initial investment in CNC technology may seem high, the long-term savings are substantial. The precision and reduced waste associated with CNC machining lead to lower production costs, making it a cost-effective choice in the long run.
Industries Benefiting from CNC Turning Parts Manufacturing
The applications of CNC turning parts manufacturing are virtually limitless. Here are some industries that have significantly benefited:
- Aerospace: The aerospace industry demands precision-engineered parts that can withstand extreme conditions. CNC turning enables the production of complex components necessary for aircraft and space vehicles.
- Automotive: Manufacturers in the automotive sector rely on CNC turning to create parts such as engine components, gears, and fasteners, which require high precision and durability.
- Medical Devices: In the medical field, manufacturers produce parts for surgical instruments and devices that require stringent adherence to regulatory standards, making CNC turning indispensable.
- Electronics: Electronics manufacturers use CNC turning to create housings and components that fit tightly and work efficiently in various devices.
The CNC Turning Process: Step-by-Step
Understanding the process behind CNC turning can help clients appreciate the complexity and skill required to produce high-quality components. Here's a detailed breakdown:
Step 1: Design Development
The first step in CNC turning is design development, where engineers and designers create a detailed CAD (computer-aided design) model that outlines the specifications, dimensions, and tolerances required for the component.
Step 2: Programming the CNC Machine
Once the design is finalized, the next step is to convert the CAD files into G-code, the language that CNC machines understand. This code directs the machine on how to move and cut material to produce the required part.
Step 3: Material Selection
Choosing the right material is crucial for the success of the project. Factors such as strength, weight, and corrosion resistance dictate material selection, whether it be aluminum, steel, or plastic.
Step 4: Setup and Machining
The CNC machine is set up with the chosen workpiece clamped securely. The machining begins, where the machine executes the G-code, removing material to achieve the desired shape and size through various cutting operations.
Step 5: Inspection and Quality Assurance
After machining, each part undergoes thorough inspection using precision measuring tools to ensure it meets all specifications. This quality assurance step is essential for maintaining the high standards expected from a CNC turning parts manufacturer.
Step 6: Finishing and Delivery
Finally, parts may undergo additional finishing processes such as polishing, anodizing, or coating before they are packed and shipped to the client, ensuring they arrive in pristine condition.
Why Choose DeepMould.net as Your CNC Turning Parts Manufacturer?
Your choice of CNC turning parts manufacturer can greatly influence your project's success. At DeepMould.net, we pride ourselves on our commitment to excellence, evidenced by the following attributes:
1. Advanced Technology and Equipment
Utilizing the latest CNC technology, we are capable of handling complex designs with unmatched precision, significantly reducing production times and costs. Our continuous investment in state-of-the-art machinery allows us to stay ahead in the manufacturing landscape.
2. Experienced Professionals
Our team comprises skilled engineers and technicians dedicated to achieving the highest quality outcomes. Their expertise ensures that every project is completed efficiently and effectively, adhering to the strictest industry standards.
3. Comprehensive Services
From design consultation to after-sales support, we offer a comprehensive suite of services. Our collaborative approach means we work closely with our clients to ensure that all their needs are met throughout the manufacturing process.
4. Commitment to Sustainability
At DeepMould.net, we prioritize eco-friendly practices. Our manufacturing processes minimize waste and energy consumption, contributing to a more sustainable industry future.
Conclusion: A Future Built on Precision
As industries continue to evolve, the role of the CNC turning parts manufacturer becomes increasingly vital. By partnering with a leading manufacturer like DeepMould.net, businesses can optimize their production capabilities, enhance product quality, and ensure that their components meet the demands of a competitive market.
Efficiency, precision, and adaptability are the cornerstones of modern manufacturing, and through the lens of CNC turning, we can see a pathway to a brighter future—one where innovation drives success and businesses can thrive. If you're looking for tailored solutions that meet your unique needs, do not hesitate to contact us at DeepMould.net today!