Understanding Production SLA in Business Processes
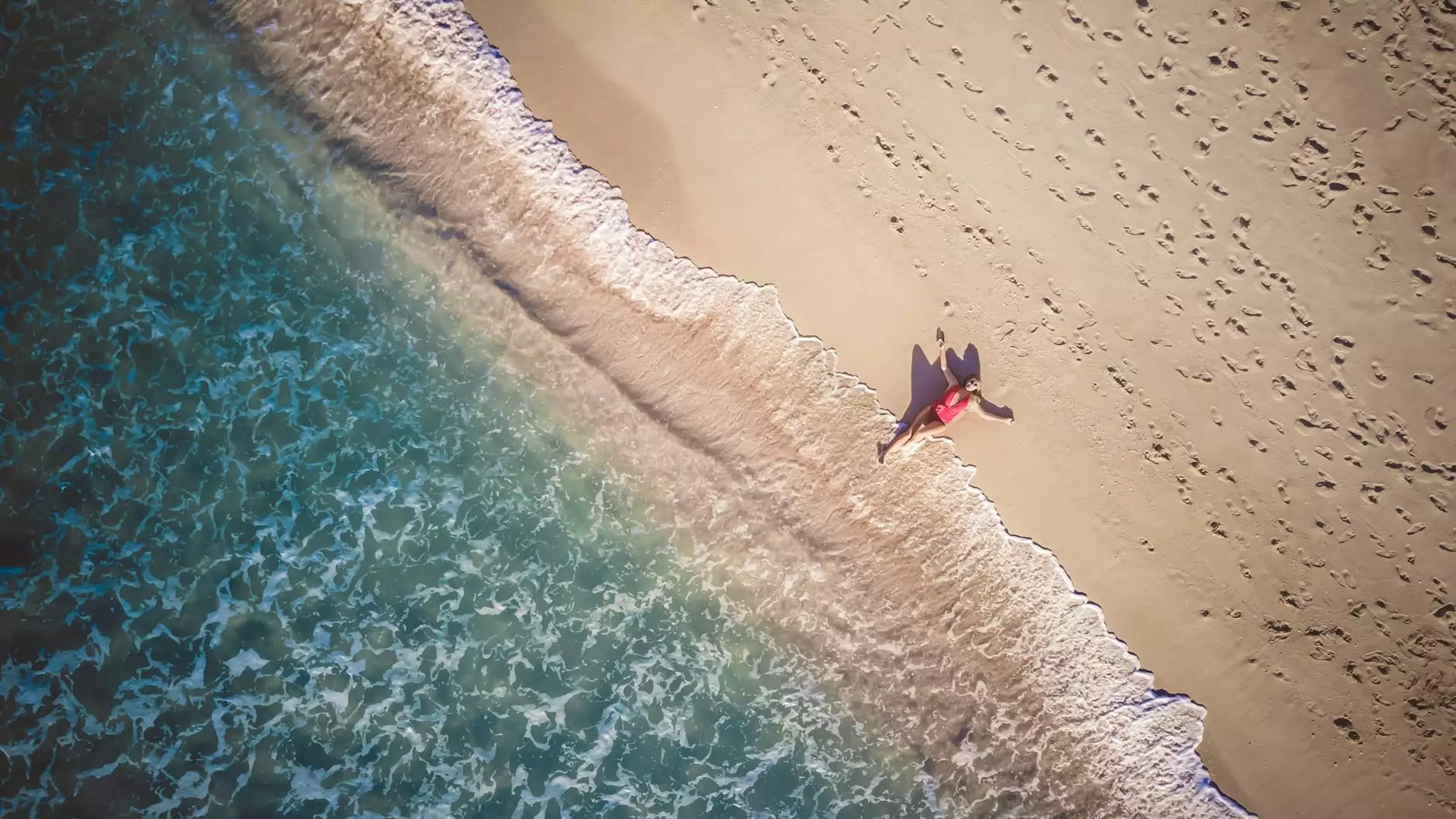
Production SLA is a critical concept in the modern business landscape that intertwines the art of creating goods and providing services within defined parameters. As businesses shift toward enhanced efficiency and superior service delivery, understanding how Production SLAs function can significantly impact operational success.
The Essence of Production SLA
In simple terms, a Service Level Agreement (SLA) defines the level of service expected from a service provider. When we talk about production SLA, we focus on agreements specifically relating to production processes—how goods are created, delivered, and supported. This becomes especially vital in sectors like art supplies, product design, and 3D printing, where end-user satisfaction is closely tied to production quality and timeliness.
Why is Production SLA Important?
Implementing a well-structured production SLA can offer numerous benefits:
- Clarity and Expectations: Both parties have a clear understanding of their roles and responsibilities.
- Measurable Standards: Performance metrics provided by SLAs help ensure accountability and can be measured against established benchmarks.
- Improved Communication: Regular updates and evaluations promote transparency and enhance collaboration.
- Quality Assurance: SLAs can include stipulations regarding quality control, ensuring higher standards in production.
- Enhanced Customer Satisfaction: Timely delivery of products can significantly improve customer satisfaction and loyalty.
Components of a Production SLA
A comprehensive production SLA includes several essential components:
1. Definition of Services
This section outlines the specific services and production processes covered by the SLA, such as:
- Manufacturing timelines
- Quality standards
- Delivery procedures
2. Performance Metrics
Clearly defined performance metrics are crucial for assessing the effectiveness of the production process. Common metrics include:
- Production lead time
- Quality assurance rates
- On-time delivery rates
3. Responsibilities of Parties
Both the service provider and the client must understand their respective responsibilities to ensure smooth collaboration. These might involve:
- Provision of materials and resources
- Communication protocols
- Reporting and accountability processes
4. Review and Reporting Procedures
Frequent reporting mechanisms to review SLA performance should be specified. This ensures both parties remain aligned in their expectations and operations.
5. Penalties and Remedies
When agreed-upon standards are not met, SLAs should detail the penalties or remedies available. This might include compensation or corrective actions required to address failures in production.
Implementing Production SLA in Art Supplies Business
The implementation of a production SLA is particularly relevant in the art supplies industry where product quality and timely deliveries can make or break customer relationships. Below are actionable steps for integrating SLAs into your business processes:
Step 1: Identify Key Products and Services
Start by detailing the art supplies you offer, from paints and canvases to specialized tools. Assess which products require stringent SLAs due to their complexity or demand.
Step 2: Determine Performance Goals
Setting clear, quantifiable performance goals is essential. Consider aspects such as:
- Time from order to delivery
- Defect rates or return rates
Step 3: Communicate with Stakeholders
Engaging with all stakeholders—suppliers, manufacturers, and clients—is crucial to align objectives and expectations regarding SLAs.
Step 4: Monitor and Revise
After implementing your production SLA, continuously monitor its effectiveness and be willing to revise it based on feedback and performance data.
The Impact of Production SLA in Product Design
In the realm of product design, having a robust production SLA is indispensable. Here’s how it can influence this category:
1. Streamlined Design Processes
A well-drafted SLA can streamline the stages of product development, ensuring designs move from conception to production efficiently.
2. Collaborative Innovation
With clear standards, designers can focus on innovation while having the confidence that production capabilities will meet their creative needs.
3. Cost Management
SLAs can aid in controlling costs associated with production delays and quality issues, enabling designers to stay within budgets.
3D Printing: The Future of Production SLA
The emergence of 3D printing technology has transformed traditional production models, necessitating the evolution of SLAs. Here’s a look at how production SLA integrates within this innovative field:
1. Customization and Flexibility
3D printing allows for high levels of customization, thus requiring SLAs that reflect the unique dynamics of each project. This flexibility must be clearly defined in the agreements.
2. Rapid Prototyping
The speed of 3D printing means SLAs need to address rapid prototyping processes, where timelines can differ significantly from traditional production.
3. Material Specifications
SLAs for 3D printing must also detail the types of materials used, ensuring compliance with quality standards and customer expectations.
Conclusion: Embracing Production SLA for Business Success
In conclusion, production SLA is not just a business necessity; it is a strategic tool that can enhance production processes across various industries, including art supplies, product design, and 3D printing. By adopting well-structured SLAs, businesses can ensure clarity, accountability, and higher customer satisfaction. The future of production relies heavily on the effective management of these agreements, making understanding and implementation of production SLAs essential for growth and sustainability.
At arti90.com, we recognize the value of operational excellence and are committed to providing our clients with the best practices for integrating production SLAs into their processes. Together, we can foster innovation, ensure quality, and enhance customer satisfaction in every project.